10 Feb
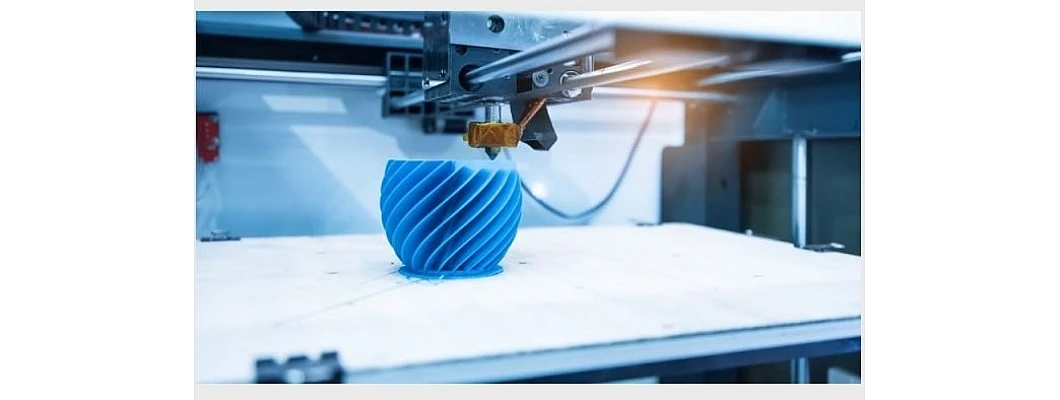
0 Comment(s)
1488 View(s)
Hello,
In this article, we are going to understand different 3D printing processes and the merits and demerits.
In this article, we are going to understand different 3D printing processes and the merits and demerits.
There are mainly 4 different types of 3D printing processes. They are:
- FDM 3D printing
- SLS 3D printing
- SLA 3D printing
- DMLS 3D printing
FDM 3D printing
- FDM is one of the most popular methods of additive manufacturing. This is a very user-friendly technology and is the go-to technology for personal use.
- In FDM, there are mainly two materials used. ABS and PLA.
- Polylactic acid (PLA) has been used by many enthusiasts as it is cheap and durable and is the most common material used for prototyping.
- Acrylonitrile butadiene styrene (ABS) when compared to PLA has some more benefits. It is more durable and has more tensile strength than PLA. They are used in heavy robotics projects.
- Both these filaments are highly recommended for FDM prototyping.
- PETG filaments are also used for FDM manufacturing sometimes.
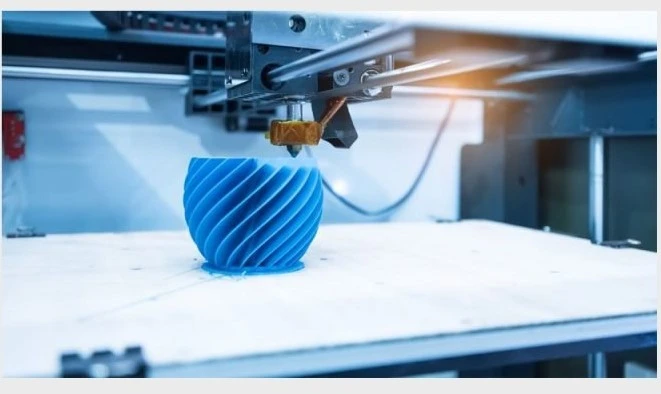
Steps involved in FDM 3D printing
- The material spool is loaded onto the 3D printer.
- The heater then starts heating up the nozzle and the bed on which the part is to be printed.
- Once the nozzle temperature and the bed temperature reach the desired value, the material starts being loaded into the extruder.
- The molten material then starts depositing on the bed and is moved appropriately by the stepper motors.
- The heater is controlled by the 3D printer and so the temperature of the nozzle and the bed is controlled by the 3D printer.
SLS 3D printing
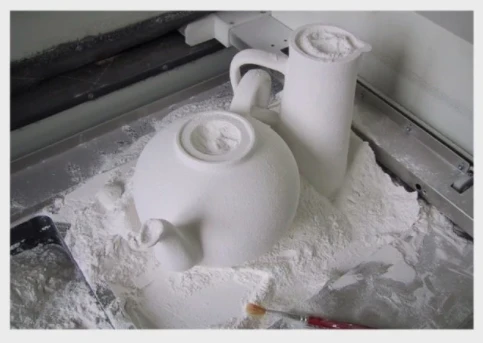
- This is the second most common method of 3D printing after FDM. The full form of this is called the Selective laser sintering.
- The filament used in this case is fine nylon powder.
- The main advantage of this process is that it does not require any supports as the part is surrounded by powder which acts as the support.
Steps involved in SLS 3D printing
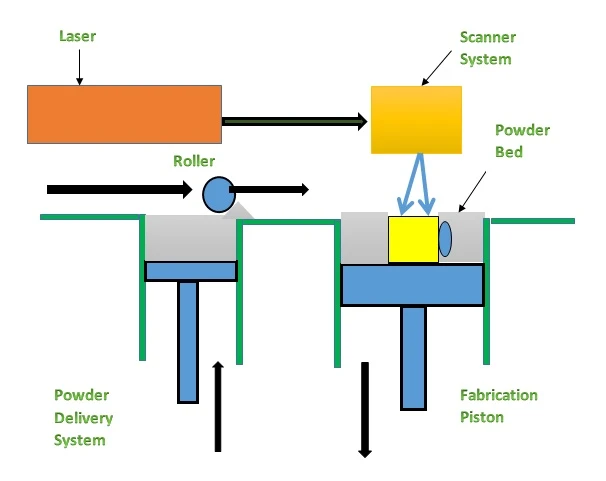
- The build chamber gets heated just below the melting point of the nylon powder.
- Now the roller shifts a small sheet of powder over to the build chamber and so the powder gets heated just below its melting point.
- A powerful C02 laser will be activated and falls on the part where the powder has to be hardened. This increases the temperature of the powder above the melting point and a bond is formed. Hardening the part which is to be printed. This process is called sintering.
- The roller now brings a new layer of powder over the old layer.
- This is how a single layer is formed in the SLS printing. The layer thickness can be changed.
- This is how layer by layer the part is printed.
SLA 3D printing
- The stereolithography method of 3D printing is very similar to SLS 3d printing. The only difference between them is that SLS uses nylon powder as filament whereas SLA printing uses liquid resin as their filament.
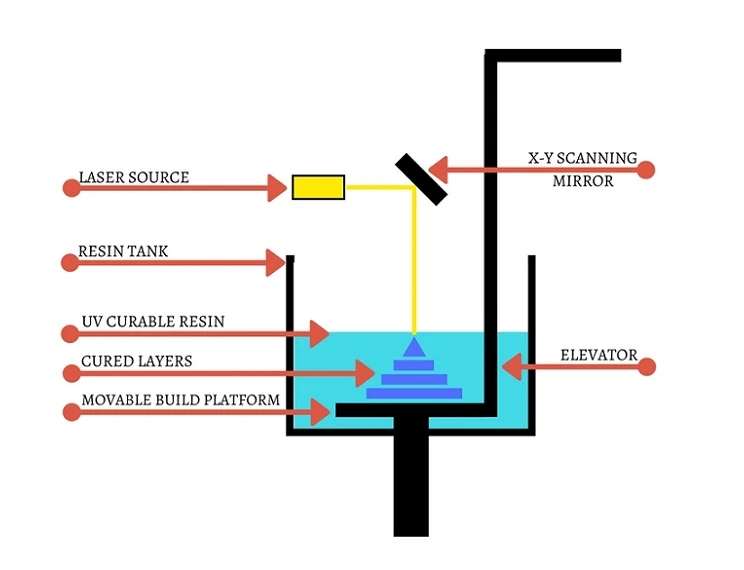
- At first, the movable platform is dipped inside the resin just enough so one layer is dipped inside the resin.
- The Laser source is activated and it falls onto the scanning mirror. The laser then gets reflected from the mirror onto the resin solidifying it.
- The mirror then traces the laser in such a way that it projects the X-Y geometry of the part. This is how a single layer is formed.
- Now the movable platform goes down by one more layer thickness and the next layer is formed.
- After all the layers are formed, the part is still soaked with liquid resin. This resin is then cleaned using isopropyl alcohol.
DMLS 3D printing
- The process of this is similar to that of SLS printing.
- The object designing process starts with 3D model designing and then the design is sent to the 3D printer.
- Once the 3D printer gets the design, it slices the design into 2D layers and then the instructions are sent to the various parts of machine.
- The laser sinters the powder as per the design
- Once the layer is sintered, the roller deposits another layer of powder onto the sintering bed.
- This process continues layer by layer until the whole object is designed.
- We can clean the excess powder by brush or air.
Leave a Comment